
Extraction of natural molecules
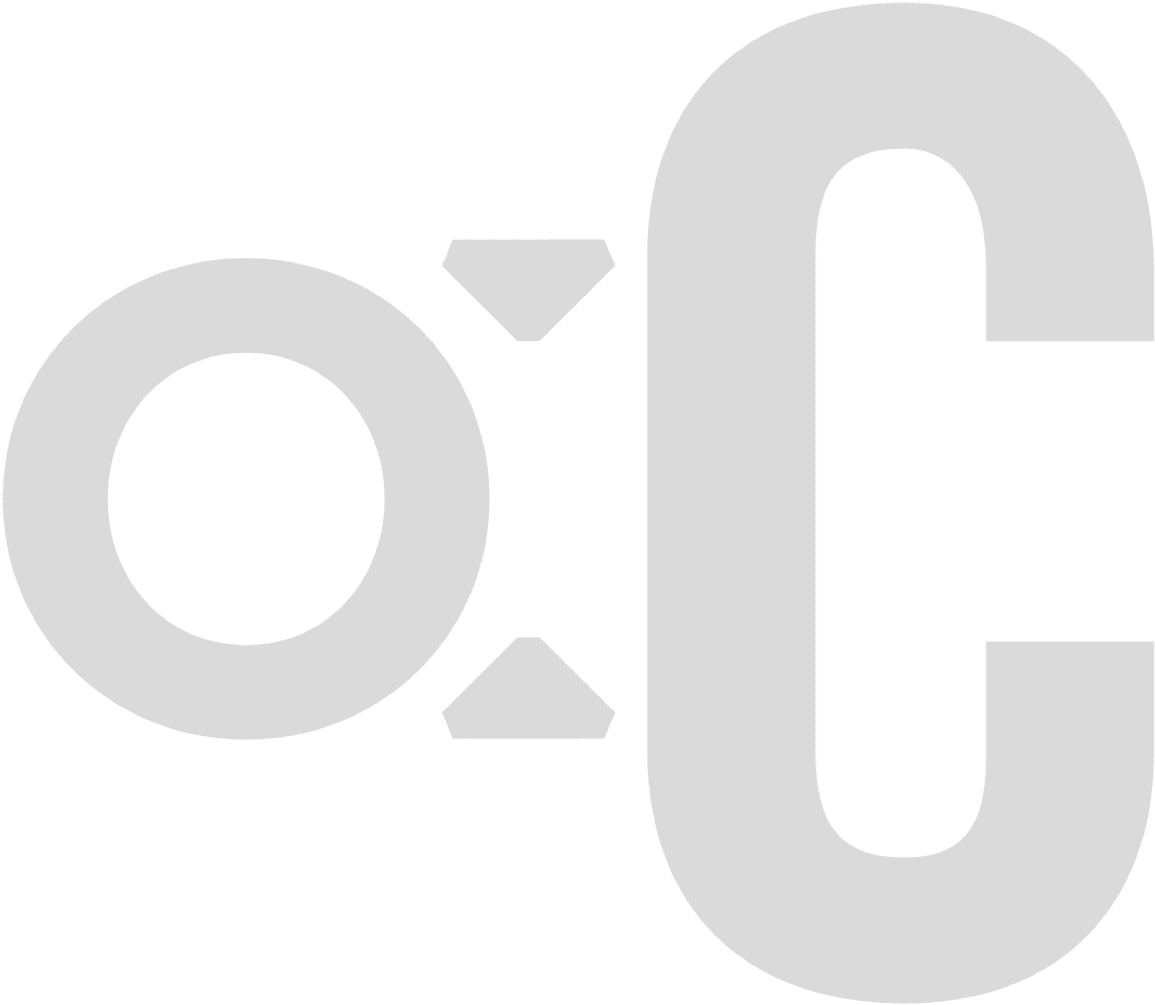
Process solutions
Since its start-up, CELSIUS build equipment for the pharmaceutical industries producing active ingredients by chemical synthesis ways.
But there are other ways for the production of Active Pharmaceutical Ingredients: the extraction of natural molecules. And the need is extended beyond pharmacy in the cosmetics, perfumery, flavorings, food supplement industries.
For this industry, CELSIUS has developed the NECTACEL process for the extraction of natural molecules using liquefied gases.
GREEN CHEMISTRY
The Greek gods on Mount Olympus possessed a natural resource with great properties, a drink that rendered them immortal: nectar (νέκταρ).
For mortals, CELSIUS has developed NECTACEL extraction processes and equipment.
Nature contains a wealth of molecules with very interesting properties for humans, for healing or simply for their well-being. Nature is an infinite resource for cosmetics, flavours, scents, nutraceuticals, etc.
Many organic molecules can be used for their active principles, their flavour, their odour, their nutritional properties, or for other specific properties that, when combined with others, are of great importance.
Whether sought for health, beauty or nutritional goals, CELSIUS uses plant chemistry principles to build extract, reagent, essential oil, concrete, absolute or functional ingredient production equipment.
CELSIUS builds NECTACEL facilities for solvent-based extraction of plant or animal molecules. Extraction, followed by separation of solvent from extract, are performed at atmospheric pressure, under vacuum or under pressure, either with or without stirring.
Each unit is designed for a specific matrix and extraction solvent:
- Steam,
- Water,
- Alcohol,
- Hexane, Toluene, etc
- Green solvents,
- Liquid gases.
NECTACEL extraction units are designed with CELSIUS’s chemical engineering, process engineering and thermodynamics expertise, and with a constant eye for facility safety, optimised resource management, energy savings and environmental protection.
EXTRACTION OF NATURAL MOLECULES
By extraction of natural molecules, we mean any process used to transfer molecules from a solid animal or plant substrate to a liquid phase.
Depending on the trade, the raw material is referred to as a matrix, load, solid, plant, drug, bagasse, etc. Once consumed by the extraction process, there remains a cake, spent solids, draff, marc, insolubles, inerts, residues, etc.
The following can be distinguished:
- Mechanical processes such as cold expression. The best known case is oil extraction, in which grains or kernels are mechanically compressed to extract the liquid phase that they contain. CELSIUS does not build mechanical process equipment.
- Plant chemistry processes. These processes involve chemical engineering, process engineering and thermodynamics expertise that CELSIUS possesses.
The extraction of natural molecules relates more specifically to the dissolution of the molecules of interest in a solvent.
The process involves two successive phases:
- An extraction step, during which a plant or animal matrix is intimately mixed with a solvent. The molecule of interest is dissolved in the solvent. The resulting solution may also be referred to as a liquor or filtrate. This phase is called solvation, maceration, digestion, decoction, infusion, leaching, elution, trituration, percolation, etc. depending on the trade and extraction conditions.
- A step of separation of solvent from extract. The solvent is evaporated and the residual extract can be liquid (solute), solid (crystallised), or solid in suspension. Depending on the extract, this phase is referred to as evaporation, boiling, desolvation, crystallisation, etc.
The extraction process can also be used with the opposite goal of extracting an undesirable molecule from the matrix, such as for example in the case of degreasing, the noble product being the refined matrix.
SOLVENT SELECTION CRITERIA
An essential step in developing an extraction process is selecting the appropriate solvent. What are the criteria behind this choice?
The criteria entering into the choice of a solvent are as follows:
- The solvating power of the desired molecule. This criterion involves notions of polarity or ionic character.
- The solvent’s ability to cross the membrane of the cells in the matrix. Small sized molecules penetrate more easily through cell pores.
- The thermodynamic properties that define the operating conditions and technologies leveraged by the equipment.
Solvent selectivity is a secondary criterion in the choice of solvent. The aim is to extract only the molecule of interest from the matrix, leaving any undesirable molecules behind. This criterion is only secondary however, as the various extracted species can be separated during the subsequent purification phase.
The ethical choice of a solvent and an extraction process is also based on notions of:
- The use of renewable sources and a “green”, non-aggressive and, at the least, recycled solvent,
- With low energy requirements,
- Based on a process operating at a temperature that does not degrade the product.
EXTRACTION PROCESSES
Extraction processes differ depending on whether the solvent is gaseous, solid, liquid or supercritical:
1. Hydrodistillation:
In this process, the extraction solvent is water vapour that entrains the molecule of interest by forming an azeotrope. The extracted gaseous solution condenses in a mixture of two non-miscible liquid solutions, one aqueous and the other organic. The organic solution contains the molecule of interest.
This process is used to extract essential oils. It is limited to extracts that support vapour temperature.
2. Cold enfleurage:
In this process, the solvent is solid and the extraction product is a solid solution. We can mention the case of cold enfleurage, in which flower petals are placed by hand on a layer of grease. This process is difficult to industrialise.
3. Liquid solvent extraction:
Many liquid solvents are used at both the laboratory and industrial levels:
- – Water,
- – Alcohols,
- – Hexane, Toluene, etc.
These solvents are liquid during the extraction phase, under normal temperature and pressure conditions. For the solvent and solute separation phase, they must be brought to gaseous state, either by increasing the temperature, reducing the pressure, or by combined action of the two.
The process is implemented taking the following into consideration:
- – The temperature during the solvent evaporation separation phase. In particular, in the case of water extraction at atmospheric pressure, the extract must not break down at the boiling point.
- – The presence of potentially harmful residual solvent (hexane or toluene) dissolved in the extract.
- – The need for recycling in the case of an expensive or harmful solvent.
4. Liquefied gases:
Liquefied gases are solvents in gaseous state under normal temperature and pressure conditions.
The advantages of this technique are as follows:
- Compared to steam, the ability to work at ambient temperature to avoid damaging the product.
- Compared to certain solvents, the ability to use a solvent that is inert relative to the product, or even an environmentally “green” solvent.
- Compared to supercritical CO2, the ability to work at a relatively low pressure and without the need for mechanical equipment.
The general schematic is that of liquid solvent extraction, evaporation, condensation and solvent recycling:
The process is implemented through the following successive phases:
- an extraction phase, during which the raw material is placed in contact with the liquid solvent.
- a separation phase, after transferring the solution obtained to the evaporator. The solvent evaporates in the evaporator, is condensed in the atmospheric condenser and is collected in the storage tank. In this isobaric and isothermal process, the solvent is evaporated then condensed under the same temperature and pressure conditions.
- an evaporator and extractor vacuum application phase, during which the solvent is evaporated to achieve separation in the evaporator on the one hand and to desorb the solvent from the solid substrate on the other hand. For the spent raw material, this is a drying operation, at heat and under vacuum, to completely recycle the solvent. At the vacuum pump discharge, at atmospheric pressure, the residual gaseous solvent is condensed on the cold spot according to the following general schematic:
At each moment, in the extractor, in the evaporator, in the condenser and in the storage tank, the solvent is at evaporation equilibrium:
- – By providing calories to the extractor, the matrix and solvent are brought to the optimum extraction temperature. The pressure is that of equilibrium.
- – By providing calories to the evaporator, the solvent evaporates.
- – By providing frigories to the condenser, the solvent condenses.
The liquefied gas extraction process and system, with solvent recycling and without circulation pump, have been patented by CELSIUS.
The main thermodynamic characteristic governing the choice of solvent is vapour pressure.
The solvent must:
- Be liquid in the extractor at the near-ambient extraction temperature, without the need to increase the pressure to excessive values for the equipment (extraction phase). In practice, the vapour pressure must not exceed 10 bar at a temperature of 35°C.
- Possess a condensation temperature at atmospheric pressure that can be reached with conventional refrigeration resources (drying phase). In practice the condensation temperature must be higher than -30°C at atmospheric pressure.
These two criteria are economic optimisation criteria in an industrial context.
Two gas families that are inert with respect to the extract are considered:
- Alkanes.
- HFCs, hydrofluorocarbons, authorised refrigerant gases.
The following diagram lists the vapour pressures of the main liquefied gases compared to conventional solvents:
This diagram allows the solvent to be selected according to the above-mentioned criteria:
Liquid gas | Butane C4H10 |
R134a 1.1.1.2 tetrafluoroéthane C2F4H2 |
Boiling point at Patm | -0.5°C | -26°C |
Vapour pressure at 35°C | 2,3 barg | 7,9 barg |
From a technology point of view, the operating conditions are easier to achieve for butane, and butane is classed as a “green” solvent. The use of butane, however, generates an ATEX zone.
On the Mollier diagram for butane shown below, the solvent’s progress during extraction and evaporation is shown.
In this isobaric and isothermal CELSIUS process, solvent evaporation and condensation are performed under the same temperature and pressure conditions. No pump or solvent compressor is required to complete the cycle, nor for solvent recycling or injection.
For tetrafluoroethane (TFE or R134a) extraction, the operating pressure is slightly higher, as shown in the following Mollier diagram:
To fully understand the benefits of the CELSIUS process, the above Mollier diagrams should be compared to those of the Mollier processes described in the following chapters.
Moreover, for the separation phase, liquefied gas extraction is also better than conventional solvent extraction.
Due to the evaporating temperature and solvent/solute phase diagram differences, it is easier to separate the solute from a liquefied gas than from a conventional organic solvent.
The industrial property of the described process and system is protected by patent.
The applications of the liquefied gas extraction process are studied in a confidential manner for CELSIUS customers. The main aim is to extract molecules for use as pharmaceuticals, cosmetics, flavours, scents, nutraceuticals, etc.
5. R134a extraction using a refrigerating unit:
This same tetrafluoroethane (TFE or R134a depending on refrigeration naming conventions) can also be used as an extraction solvent, but according to a totally different process.
In this case, the refrigerant property of the fluid is used: the solvent follows a Carnot cycle by means of a gas compressor, according to the path shown on the following Mollier diagram:
Small-scale applications have been implemented using repurposed refrigerating units. In addition to the complexity of its mechanical parts, this process suffers from the additional energy consumption of the gas compressor.
6. Supercritical CO2 extraction:
When this extraction process was discovered, supercritical CO2 appeared as a highly promising solvent:
- CO2 is completely inert, safe and cheap.
- In supercritical state, it acts as an excellent solvent.
- Extraction and separation are performed at ambient temperature, an advantage when working with heat-sensitive molecules.
CO2 is used:
- in the supercritical phase during extraction, at a pressure in excess of 72 bar (in practice at between 300 and 500 bar).
- in the gas phase during separation, at between 20 and 60 bar.
The solvent follows a Carnot cycle, thanks to a liquid solvent pump, according to the following Mollier diagram.
The maximum operating pressures of the equipment increase the investment costs of a supercritical CO2 extraction unit and limit equipment capacity.
In practice, the supercritical CO2 extraction process is limited:
- to reduced size pilot units for which an extractor can be created by using an extractor machined from stainless steel bar.
- to dedicated very large-scale units producing a high added value product full-time (e.g.: decaffeination units).
NECTACEL PRESSURISED PROCESS
The pressurized extraction process developed by CELSIUS is intended to allow the extraction of any polar or non-polar plant or animal molecules.
The investment cost, lower than for supercritical CO2 and requiring a less complex infrastructure, enables extraction units to be implemented at the raw material production site, thus processing the raw material without incurring any additional transport costs.
Liquefied gas extraction:
The use of liquefied gas as an extraction solvent presents many advantages:
- The liquefied gases used are chemically inert relative to the matrix and extract. They are safe and can be inhaled or ingested by living organisms.
- The extraction and separation phases are performed at ambient temperature, which is beneficial for heat-sensitive or heat-oxidizable molecules.
- The solvent molecules are small and can readily pass through cell membranes.
- The solvation properties can be extended by using a co-solvent with complementary ionic characteristics.
- Extraction and separation are performed at a relatively low pressure (less than 10 barg), with no technological capacity limitations for the equipment used.
BUTANE, HFO1234ze and DME (dimethylether) are the most commonly used liquefied gases in nectaCel extractors.
CELSIUS builds its extractors:
- With no mechanical pumping parts: neither circulation pump nor gas compressor (with the exception of a vacuum pump to complete the drying of the residue at the end of the process).
- With energy requirements limited simply to solvent evaporation and condensation.
- With virtually all the solvent recycled.
- According to a process developed and patented by CELSIUS.
Depending on its nature, the extract is obtained as a liquid, powder, suspension or as a solution in a co-solvent. The spent matrix is dried before the extractor is reopened.
The extraction process can also be used with the opposite goal of extracting an undesirable molecule from the matrix, the noble product being the refined matrix.
CELSIUS studies your needs with you. Qualitative tests can be performed by Plateforme d’Eco-Extraction de Valréas using pilot extractor of 1 liter capacity.
NECTACEL extraction facilities are assemblies:
- comprising the equipment required for extraction, filtration, solvent evaporation, extract concentration, condensation, storage and solvent recycling,
- designed and assembled on a turnkey basis in CELSIUS’s own workshops compliant with DESP 2014/68/EU and ATEX 2014/34/EU (in the case of butane or DME), with CE
- multi-purpose or dedicated to a single product, at the laboratory or industrial scale.
Solvent extraction process applications are studied in a confidential manner for CELSIUS customers.
Fields of application
Cannabidiol extraction from hemp
Artemisinine extraction from artemisia annua
Oil extraction from oil cakes
Need an expert ?
Tell us what you need using our contact form
Our references
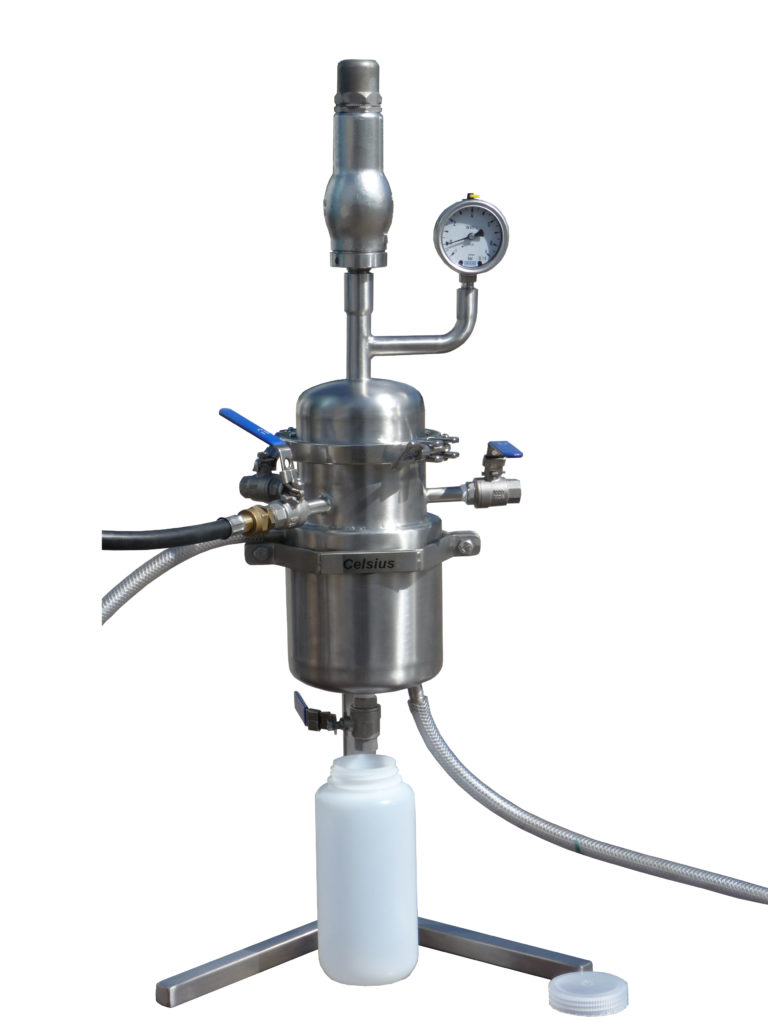
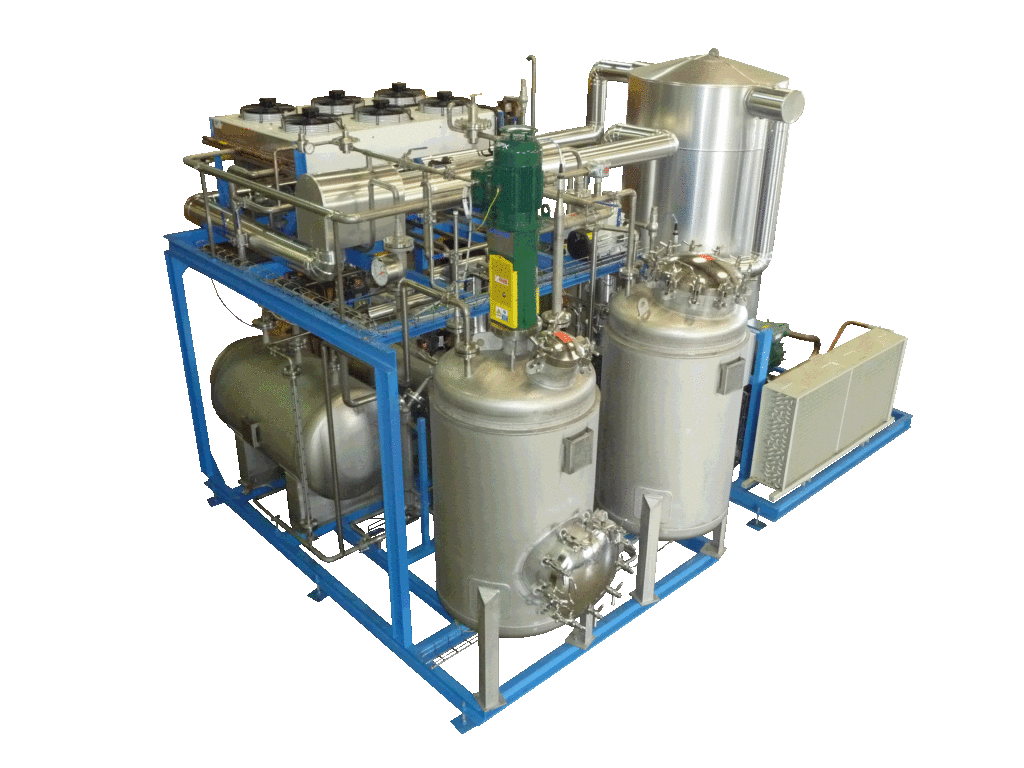
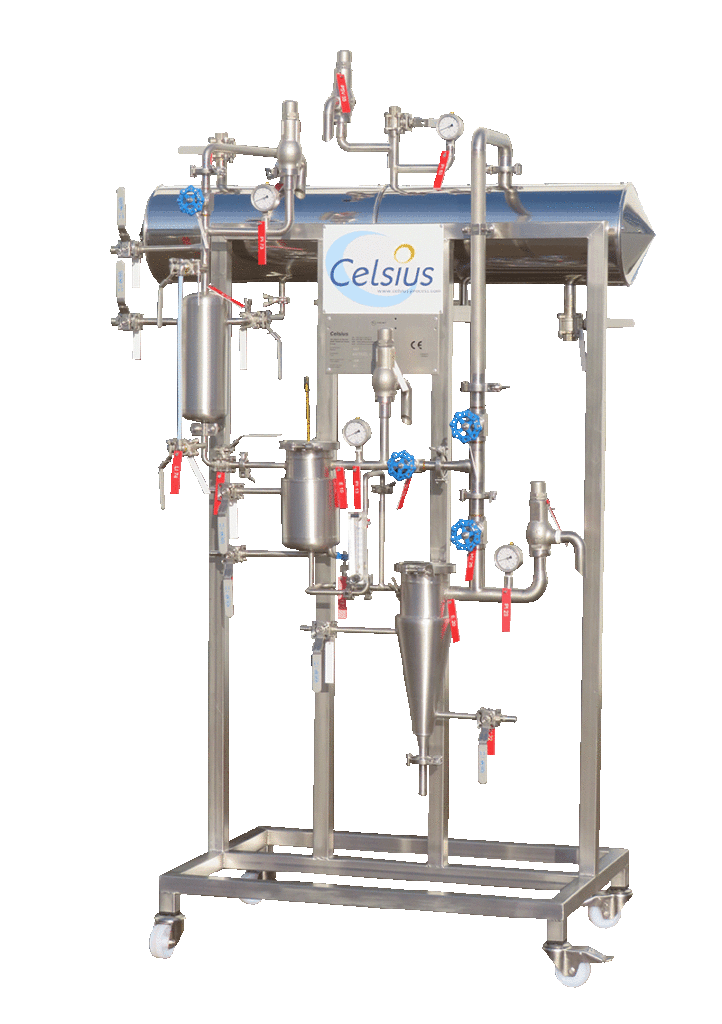
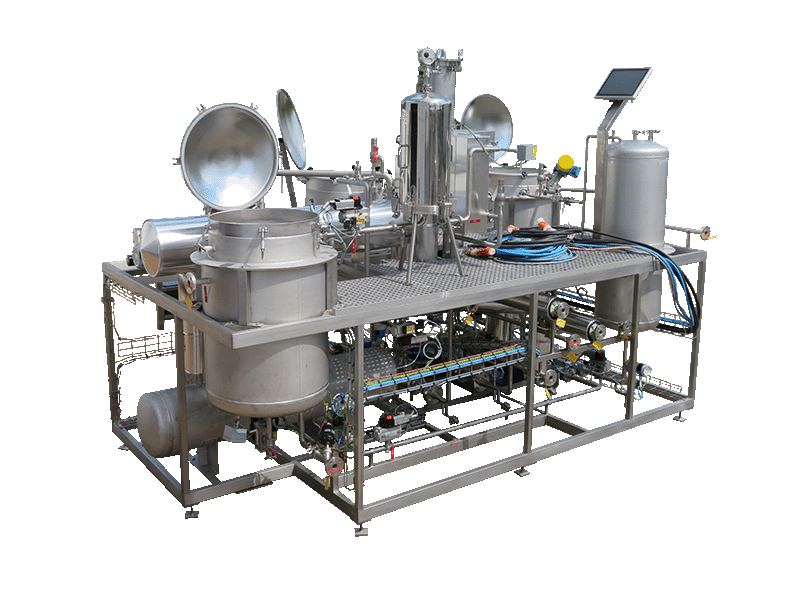
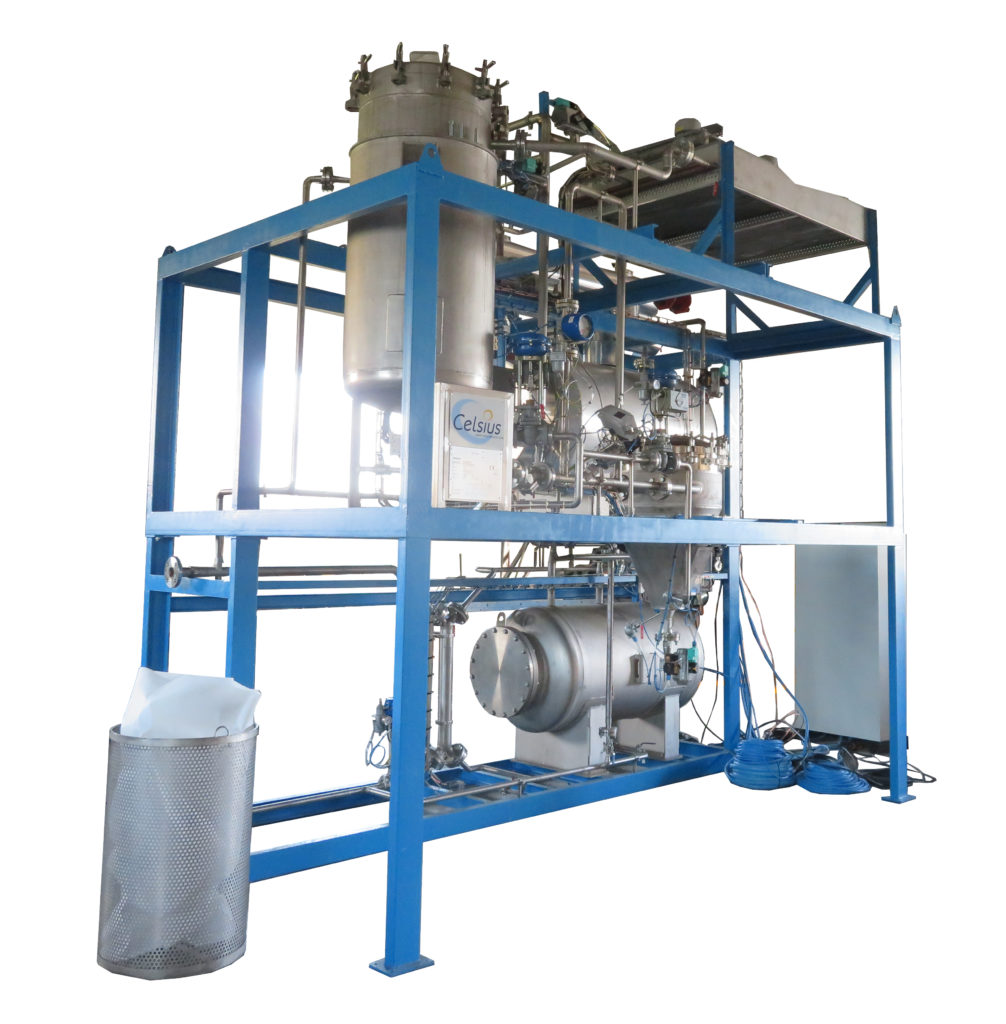
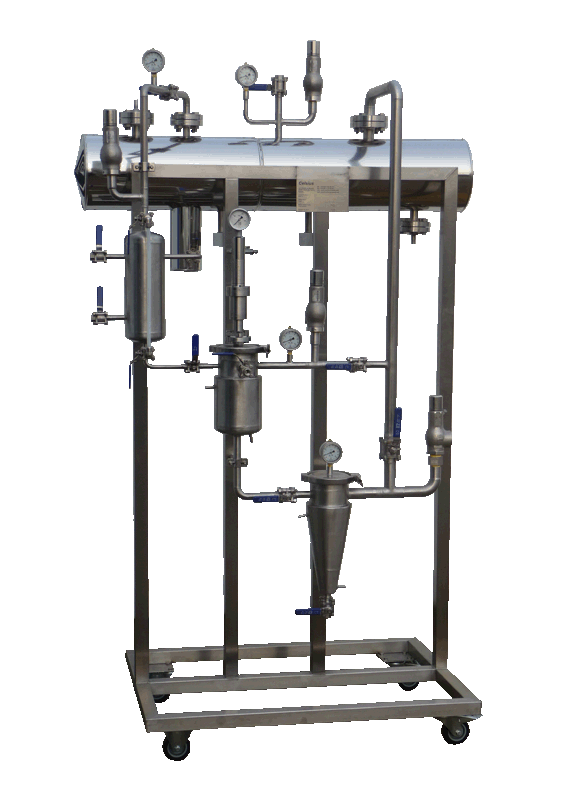
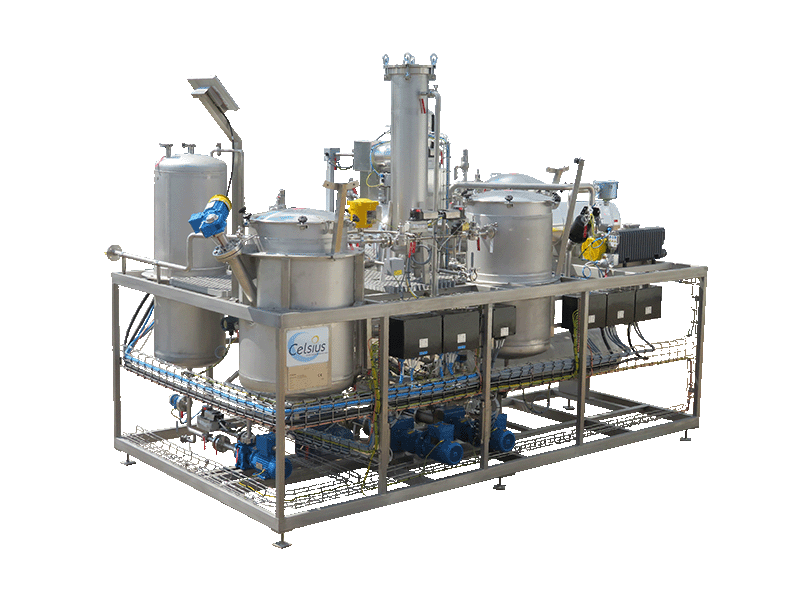
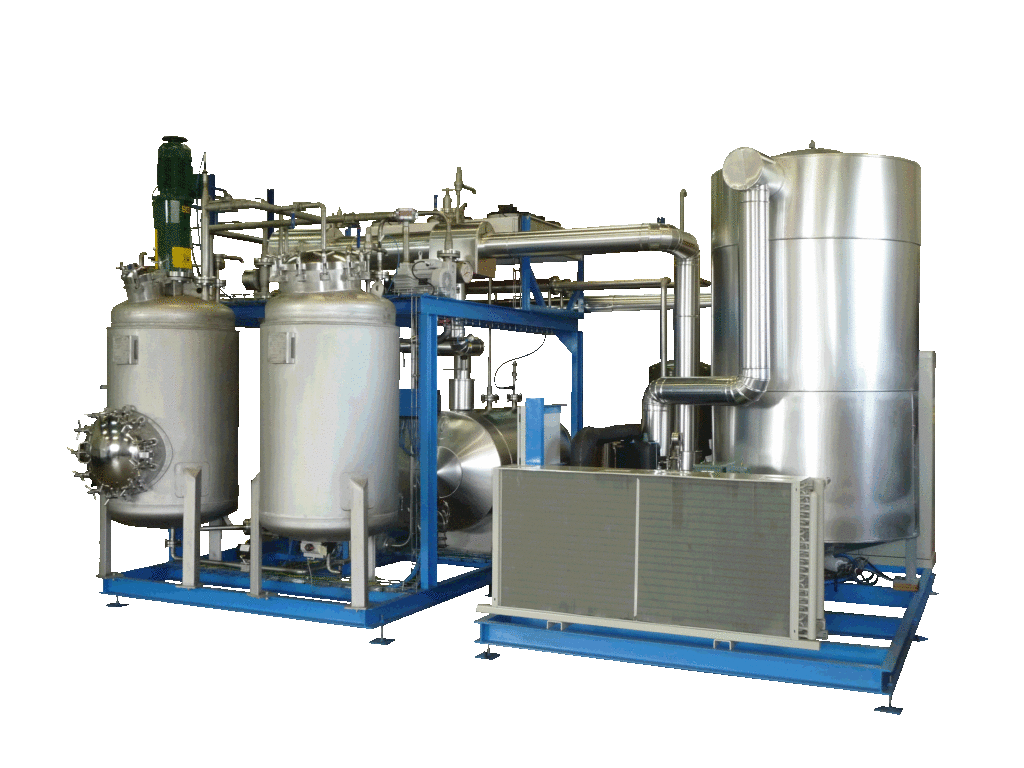
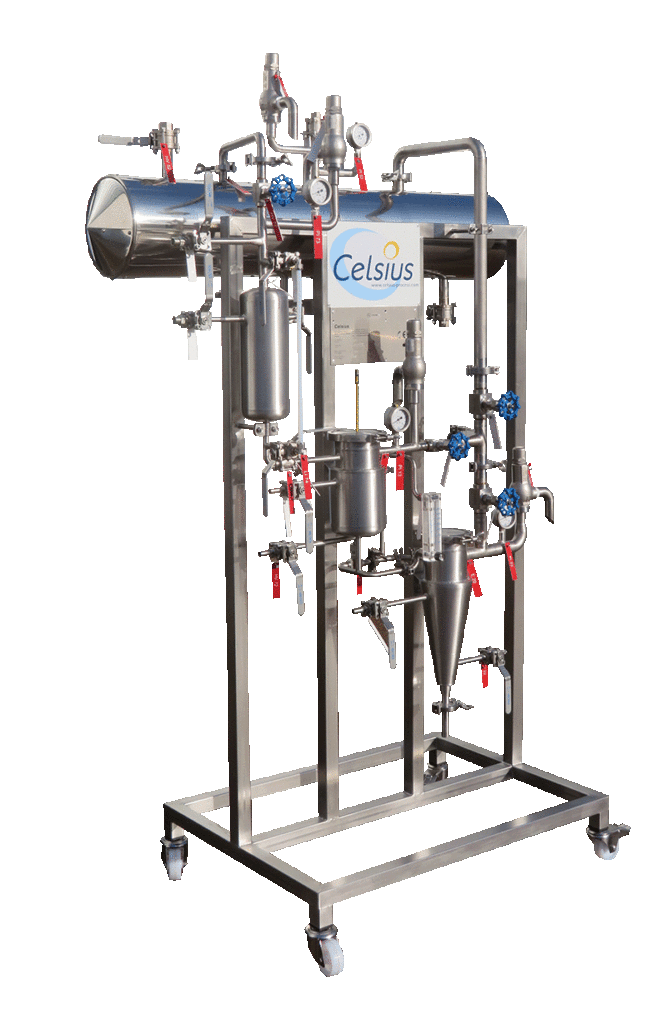
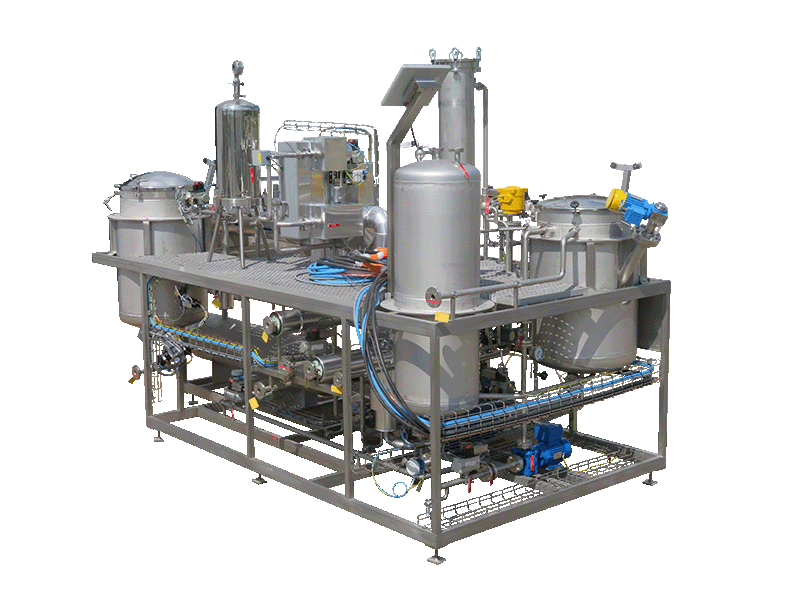
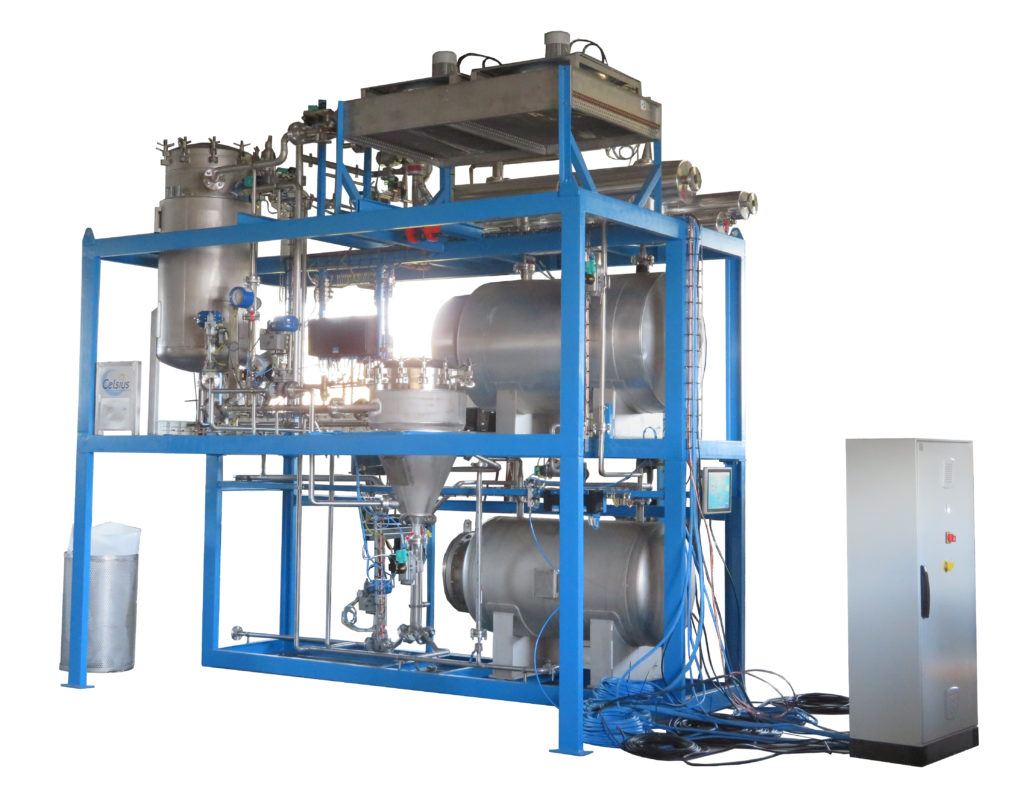
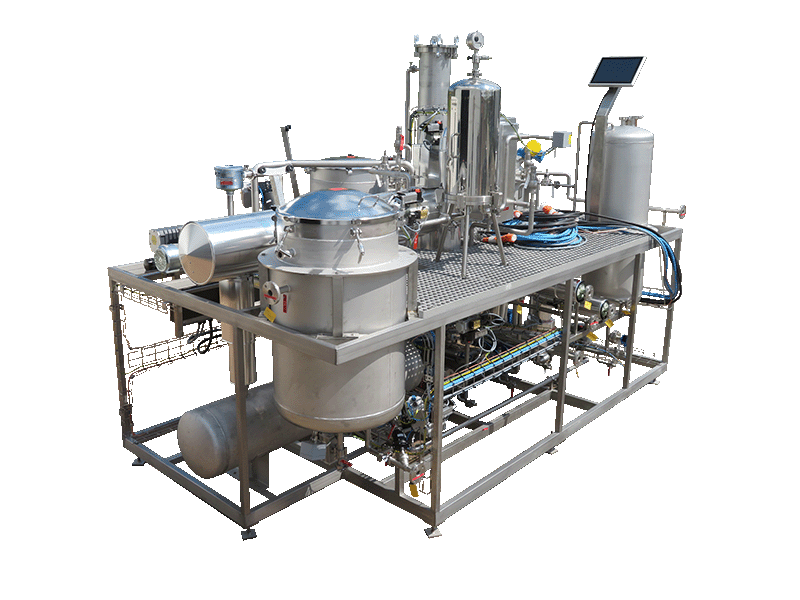
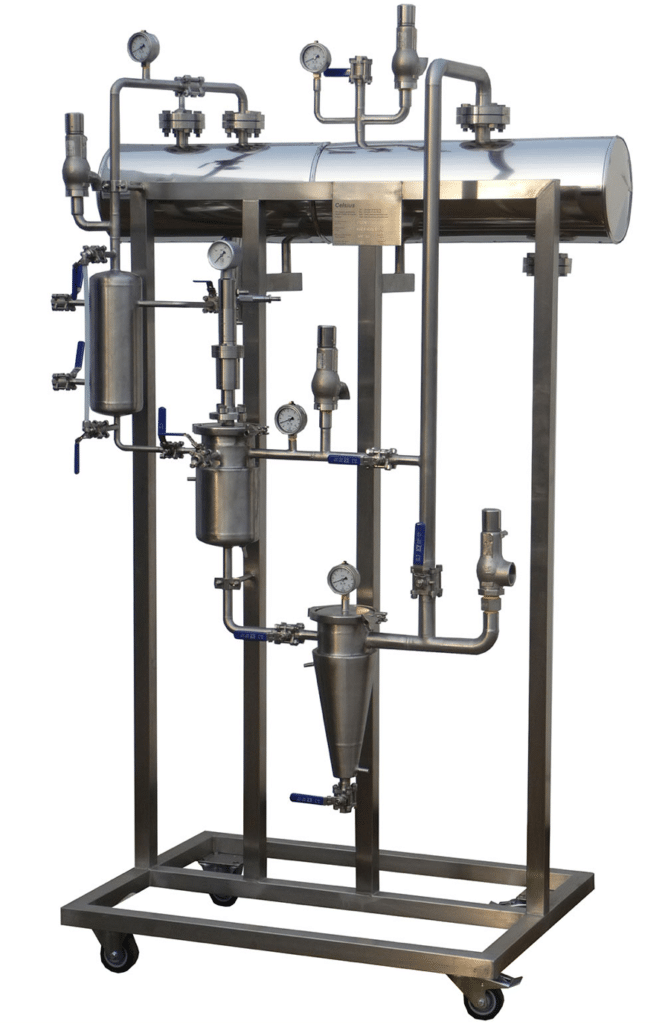
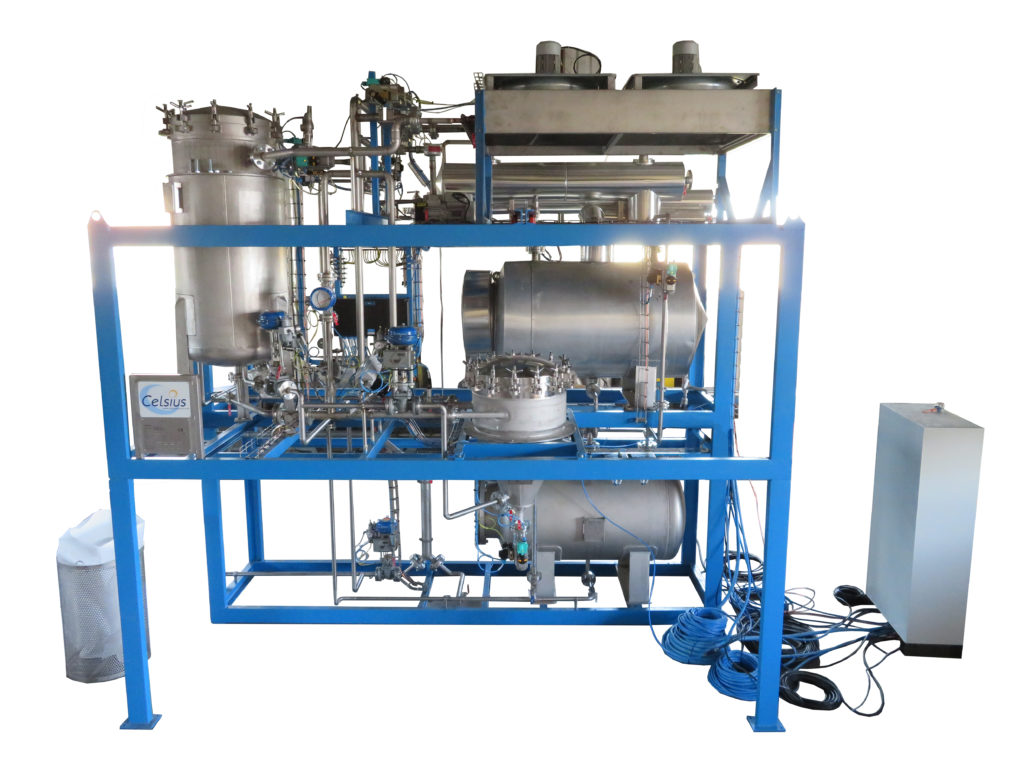
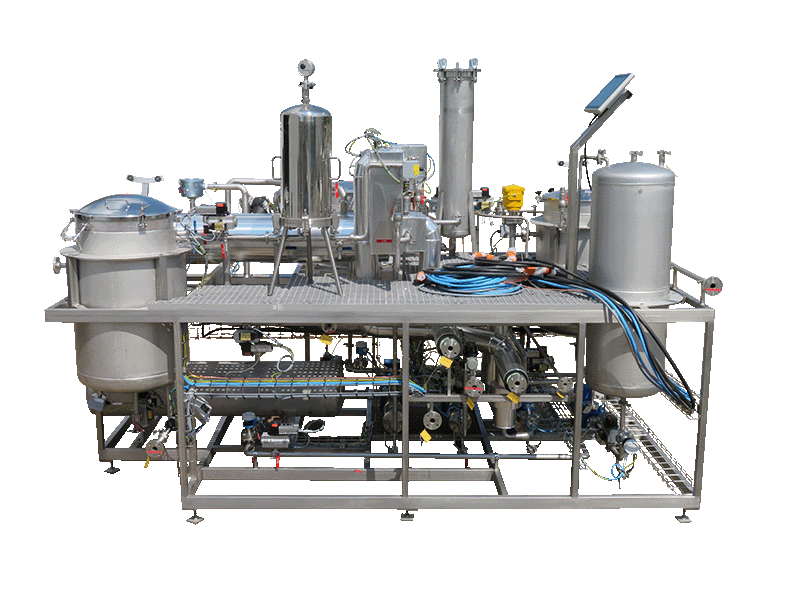
UNIVERSITA di Torino (Italy)
NECTACEL pilote extraction unit, capacity 1 litre
2013PLATEFORME d'ECO-EXTRACTION de VALREAS (France)
NECTACEL pilote extraction unit, capacity 1 litre
2016ITC (USA)
NECTACEL extraction unit, 200 litres capacity
2020KKI Latvian State Institute of Wood Chemistry - Riga (Latvia)
NECTACEL pilote extraction unit, capacity 1 litre
2021MARIPHARM - Rotterdam (Nederlands)
NECTACEL pilote extraction unit, capacity 1 litre
2021EDEN ECOSYSTEMS - Forcalquier (France)
Extraction unit using ultrasonic assistance, capacity 200 litres
2021Ressources
Many articles have been published in scientific journals. We communicate publications that compare our extraction process to other processes, publications in which we have participated.
For copyright reasons, we only communicate the first page of the article published in “Techniques de l’Ingénieur”.
In addition, it may be difficult to find the properties of the solvents used in the extraction units. You can download here the enthalpy diagrams, called Mollier diagrams, of these solvents.
Scientific publications
An original approach for lipophilic natural products extraction: Use of liquefied n-butane as alternative solvent to n-hexane
Download linkFeasibility of using liquefied gas HFO-1234ze (trans-1,3,3,3-tetrafluoroprop-1-ene) as an alternative to conventional solvents for solideliquid extraction of food ingredients and natural products
Download linkPotentialities of using liquefied gases as alternative solventsto substitute hexane for the extraction of aromas from freshand dry natural products
Download linkA review of sustainable and intensified techniques for extraction of food and natural products
Download linkTechniques de l'Ingénieur
Gaz liquéfiés comme solvants alternatifs appliqués à l’éco-extraction du végétal
Download linkEnthalpy diagrams
CO2
Download linkDimethyl ether
Download linkEthanol
Download linkn-Butane
Download link1112 Tetrafluoroethane
Download linkHFO1234ze
Download linkCelsius Process is also...
Discover one of our key process : Temperature regulation